The 50 ton overhead crane, a stalwart in heavy industrial settings, serves as the backbone of efficient material handling and lifting operations. To ensure its continued reliability, precision, and, above all, safety, a robust maintenance regimen is imperative. In this comprehensive guide, we delve into the essential aspects of overhead crane 50 ton maintenance, outlining key practices, inspections, and considerations that contribute to the longevity and optimal performance of these powerful lifting machines.
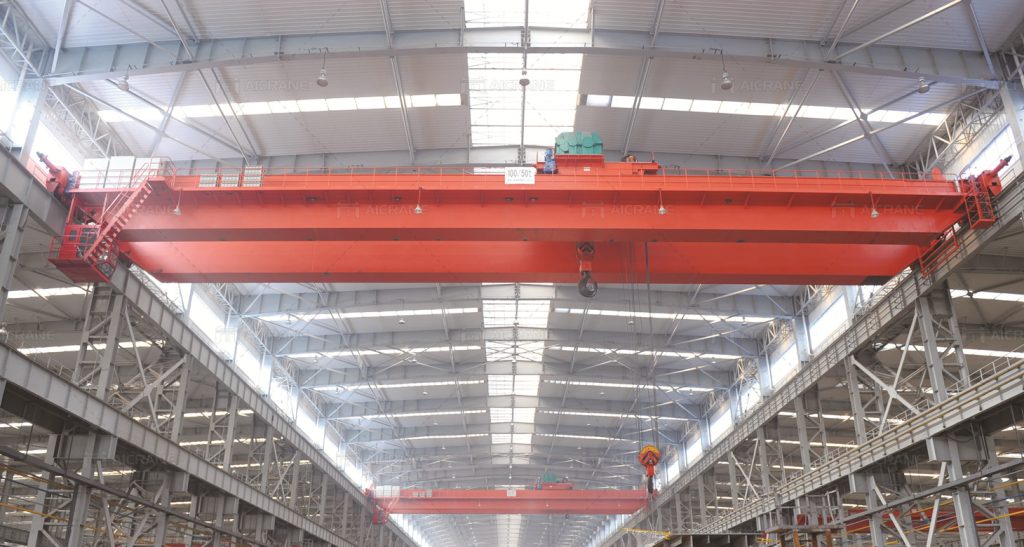
Routine Inspections: The Foundation of Preventive Maintenance
Visual Inspections
Initiate a routine of visual inspections to assess the overall condition of the 50 ton overhead crane. Examine structural components, such as the bridge, trolley, and runway, for signs of wear, corrosion, or deformities. Pay special attention to welds and connections, ensuring they remain secure. Visual inspections provide an initial assessment of the crane’s health and facilitate the identification of potential issues before they escalate.
Electrical Systems Check
Inspect the electrical components of the overhead crane, including wiring, connections, and control panels. Look for any signs of frayed wires, loose connections, or corrosion. Test the functionality of control devices, limit switches, and emergency stop features. A thorough check of the electrical systems is crucial for ensuring safe and reliable crane operation, minimizing the risk of electrical failures during lifting operations.
Lubrication: Preserving the Fluidity of Movement
Regular Lubrication Schedule
Establish a regular lubrication schedule for the moving parts of the 50 ton overhead crane. Lubricate critical components such as gears, bearings, wheels, and ropes to reduce friction and wear. The lubrication process not only enhances the fluidity of movement but also acts as a protective measure against corrosion and premature component deterioration. Refer to the manufacturer guidelines for recommended lubricants and intervals.
Inspect Lubrication Points
During routine maintenance, inspect all lubrication points to ensure that grease or oil is applied uniformly. Pay attention to any signs of over-lubrication or insufficient lubrication, as both can lead to operational issues. Adequate lubrication contributes to the smooth and efficient functioning of the crane, minimizing wear on crucial components and extending their operational lifespan.
Structural Integrity Checks: Ensuring Safety in Operation
Load Testing
Regular load testing is a critical aspect of overhead crane maintenance, especially for a 50 ton heavy duty crane designed to handle heavy loads. Conduct load tests to verify the crane’s lifting capacity and stability under realistic conditions. This process ensures that the crane can safely handle the specified loads without compromising its structural integrity. Load testing provides valuable data for assessing the crane’s performance and identifying any potential issues.
Inspection of Hooks and Lifting Devices
Thoroughly inspect hooks, lifting attachments, and any associated hardware for signs of wear, deformation, or cracks. The condition of these components is crucial for the safe lifting and lowering of loads. If any issues are identified, promptly replace or repair the affected parts to maintain the integrity of the lifting system.
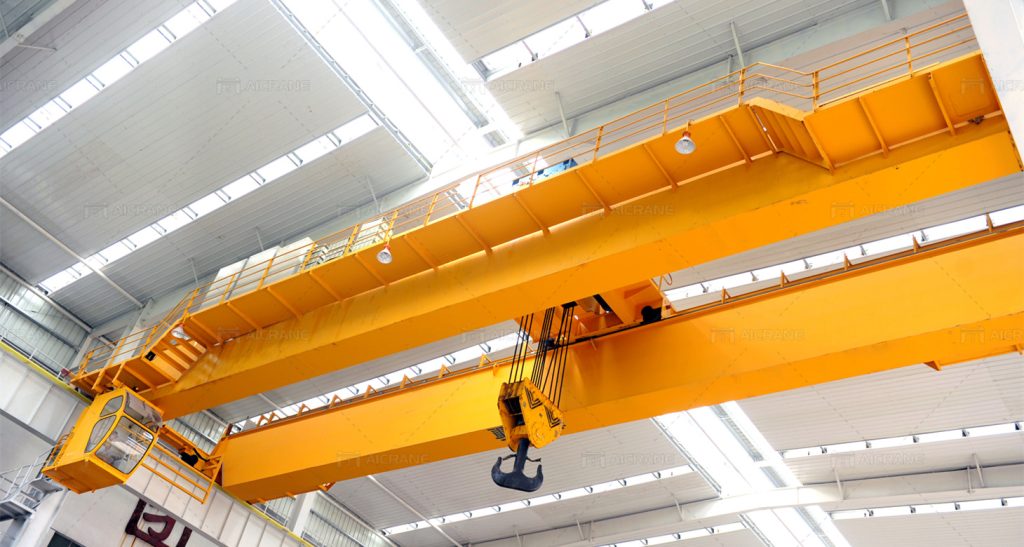
Electrical System Maintenance: Safeguarding Control and Safety Features
Inspect Electrical Wiring
Regularly inspect the electrical wiring throughout the overhead crane system. Look for signs of wear, damage, or exposure. Damaged wiring can compromise the functionality of control systems and pose safety risks. Address any issues promptly, and replace damaged wiring to maintain the electrical integrity of the crane.
Calibration of Control Systems
Ensure that the control systems, including pendant controls and remote control devices, are calibrated correctly. Calibration is essential for accurate and precise control of the crane’s movements. Regularly test and calibrate these systems to maintain control accuracy and prevent deviations that could lead to operational errors.
Operator Training and Safety Reviews: Empowering the Human Element
Operator Training Programs
Invest in comprehensive training programs for crane operators. Well-trained operators are essential for safe and efficient crane operation. Training should cover the proper use of controls, load handling procedures, and adherence to safety protocols. Regular refresher courses can help operators stay abreast of best practices and safety guidelines.
Safety Reviews and Audits
Conduct periodic safety reviews and audits to assess overall compliance with safety standards. Evaluate the effectiveness of safety features, emergency stop procedures, and evacuation plans. Identify and address any safety concerns promptly. A proactive approach to safety reviews contributes to a culture of safety consciousness and ensures that the overhead crane remains a secure working environment.
Emergency Preparedness: Planning for Contingencies
Emergency Stop Testing
Regularly test the emergency stop functionality of the overhead crane. This involves simulating emergency scenarios and verifying that the emergency stop feature brings the crane to a halt promptly. Emergency stop testing is crucial for ensuring that the crane can be quickly and effectively stopped in the event of an emergency or malfunction.
Emergency Response Planning
Develop and regularly review emergency response plans specific to overhead crane operations. Ensure that personnel are trained on emergency procedures, including evacuation routes and first aid measures. Establish clear communication protocols for emergency situations and conduct regular drills to reinforce preparedness. A well-prepared response to contingencies minimizes the potential impact of unforeseen events.
Safeguarding Reliability and Safety
In conclusion, overhead crane 50 ton maintenance is a multifaceted undertaking that requires a proactive approach to prevent issues and ensure the long-term reliability and safety of these powerful lifting machines. Routine inspections, lubrication, structural integrity checks, electrical system maintenance, operator training, and emergency preparedness collectively form a comprehensive maintenance strategy. By prioritizing precision and safety, organizations can maximize the operational efficiency of their 50 ton overhead cranes, contributing to seamless material handling operations in diverse industrial settings.